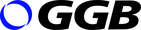
Contact Details:
GGB North America
700 Mid Atlantic Parkway
Thorofare
NJ
08086
United States of America
Tel: +1 856 686-2642
Fax: +1 856 848-5115
Send Enquiry | Company Information
Bearing Cartridges Eliminate Lubrication Downtime
Product News Tuesday, August 23, 2011: GGB North America
No one wants machine downtime, even to lubricate a joint. When industrial vehicles are down, especially for a difficult repair, the situation reduces the owner’s bottom line. One such time-consuming and costly repair is bearing replacement.
To address such situations, GGB, formerly Glacier Garlock Bearings, developed a sealed bearing cartridge that gives off-road OEMs an alternative to conventional greased bronze, hardened steel and rolling-element bearings for demanding applications.
Savings come because the equipment does not have to be taken out of operation to be serviced. “The cost of a lubrication system is eliminated and maintenance costs are reduced,” said Charles Woods, global filament-wound products manager. “Plus, the equipment owner does not have to use a potentially environment-harmful lubricant or worry about spills.
The new sealed bearing cartridges are based on GAR-MAX™ filament-wound bearing material. Compared with a greased steel bearing, a sealed bearing cartridge can save about $525 over a five-year period, according to Woods. This reduction in cost of ownership is based on the elimination of grease labor ($187.50), bearing replacement and associated labor ($187.50), and downtime for bearing replacement ($150). For a piece of equipment containing 20 such bearings, for example, the savings over a five-year period would total $10,000.
The filament-wound bearings have a bearing surface of PTFE and high-strength fibers twisted together and encapsulated by a high-temperature epoxy resin enhanced with a self-lubricating additive. High-load capability is up to 90,000 lbs/in2. or 620 MPa. The bearings exhibit good tolerance to shock and edge loading, and because they do not absorb moisture and swell, they provide dimensional stability as well.
GGB worked with major off-highway OEMs and the Advanced Manufacturing Institute (AMI) at Kansas State University to prove that its sealed bearing cartridges outperform greased, hardened-steel bearings in several applications. The mission of AMI is to provide an array of resources to people and companies on advanced technologies. “We do this through collaborative engineering and business partnerships,” Taylor Jones, chief engineer, explains. “We use our engineering expertise to develop and transfer new technologies, as well as provide technical assistance to industry.”
“We had a client company looking for alternative solutions for pin joints in abusive applications,” noted Jones, “so the institute developed a test plan to evaluate current market offerings, such as greased hardened steel bushings, chrome-plated pins and different bearing materials. We contacted various suppliers, including GGB.”
The test conditions simulated an abusive field application and heavy contamination by combining sand, dirt and water into a thick paste. “Most lab tests use a ‘mud box’ but the contaminant can wick away during oscillating and rotating test cycles,” explained Jones. “In our test, we wanted to simulate a machine that is constantly in and out of contamination all day long. We applied the paste right on the bearings.”
The tests also focused on conditions with bearing working pressures up to 7,500 psi, oscillating motion speeds that averaged 20 degrees/second and roughly 575 cycles per hour. A baseline test determined the duration of the GGB sealed bearing test.
The average wear of the sealed bearing cartridge was 0.003 in., as compared to an average wear of 0.022 in. for the traditional bushing, though the bearing cartridge was tested about 2.5 times longer than the greased hardened-steel bushing (600,000 cycles compared to 220,000 cycles).
“If properly sealed, the ungreased GGB sealed bearing cartridge appears to be a viable alternative to a sealed and greased hardened-steel bushing in severe work environments,” said Jones. “Any OEM using the sealed bearing cartridges in its equipment should follow GGB’s recommended design practices for a successful solution.”
An outer steel casing on the sealed bearing cartridges helps with installation and durability. Greasing is not required, resulting in an environmentally friendly product.